Menu
- Home
- Company
-
Products
-
Terminal Blocks
- Din Rail Mounted Terminal Blocks
- Panel Mounted Terminal Blocks
- High Temperature Ceramic Terminal Blocks (Porcelain Connectors)
- Double Layers (Decks) Terminal Blocks
- Double Row Barrier Terminal Strips
- PCB Type Single Row Barrier Terminal Blocks
- Power Terminal Blocks
- Power Splicer Terminal Blocks
- Power Stud Terminal Blocks
- Power Splicer Stud Terminal Blocks
- Power Distribution Terminal Blocks
- Euro Type Feed Through Terminal Blocks
- Fuse Holder / Fuse Block
- Fuse Clips
- Tube Fuse
- Solid State Relay
- Insulators & Busbar Support
- Accessories
- Terminal Jumper & Barrier Jumper
- Terminal Block Quick Connector
- Buckle Clamp Strap
- Filter Specification(Terminal Blocks|Solid State Relay|Fuse Holder|Insulators)
-
Terminal Blocks
- News
- FAQ
- Contact Us
- OEM/ODM
Promotion
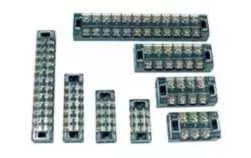
Fixed Terminal Block
TB Series Terminal Block is Panel Mounted Terminal Block, the spec is 600V, 15A / 25A / 35A with 3 / 4 / 6 / 12 Pole.
More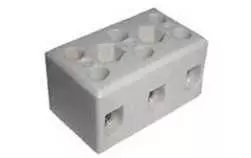
Ceramic Terminal Block
Ceramic Terminal Blocks are designed for wiring connection in high temperature condition. Spec: 15A / 20A / 50A / 65A.
MoreTERMINAL BLOCKS' SOLUTION
Based in Taiwan since 1978, SHINING E&E INDUSTRIAL CO., LTD has been a manufacturer of electrical terminal blocks and barrier strip connectors manufacturer. Since 1978, in the Power Distribution Industry, Shining E&E has been offering our customers high quality production service. With both advanced technology and 45 years experience, Shining E&E always make sure to meet each customer's demand.
Q: What are the proper Torque Values for Terminal Blocks?
A: The torque depends on the type and size of screw/hardware used in the terminal block. Torque values can be found on our spec sheet in our website
Q: How to find Accessories for the TA Series Terminal Block?
A: Use this link to our online catalog for the TA Series Terminal Block and click on the Accessary link to view listed Accessories. TA terminal block
Q:Do you have Din Rail for Din Rail mounted Terminal Block?
A:Yes,we have three Din Rails for your reference.The spec are:
- TA-001A Din Rail:Width-35mm.Material:Aluminum
- TA-001S Din Rail:Width-35mm.Material:Steel,Zinc Plated.
- TS-001 Din Rail:Width-25.5mm.Material:Aluminum.
Please let us know what Din Rail mounted Terminal Block you need,so we can recommend a suitable Din Rail for you.
Q: Which kind of End Clamp should I use with my Terminal Blocks?
A: It depends on the width of the Din Rail you are using, and the material and type of the End Clamps you prefer. For more information: http://www.shining.com.tw/1EN/ENaccessories_end_clamp_bracket.htm
Q: How can I get a quote from SHINING?
A: Our email address is: hsichin2@ms37.hinet.net
Please provide us your company profile (name, tel, fax, address, and webpage)
And let us know the parts numer, spec, quantity, and what you need, so we can contact and provide more information to you.
Q: How long is SHINING’s “Lead Time”?
A: Usually, the lead time for sample order would be 2~3 days after receiving your sample fee. For bulk order, the lead time would be 7~14 days.However, we need to double check our stock and production line.
Q:How to choose a suitable Terminal Block?
A:You can follow the“Rated Voltage,Rated Current,Wire Size,Wire quantity,Screw Size,installation method and ect”for a Terminal Block.
Our sales term will recommend a suitable Terminal Block for you if we can get these information from you.
The Terminal Strip is a connector which allows more than one circuit to connect to another circuit. A terminal block is consists of Plastic Parts and Metal Hardware Parts. In other words, it includes Terminal Block Housing (Plastic Parts), Conductor and the Screw (Metal Parts).
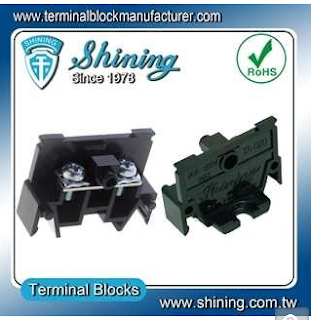
The material of conductor is brass, aluminum or other metal, and finished with nickel, tin or other material. With the conductor, the different wires can conduct each other.
![]() |
TGP-085-03A1 screw to Tab type |
The function of a screw is to fasten the wires. Also, the screw is also an electric conductor, which can connect the wire and conductor. Please note, you need to tighten the screw well when you use the terminal block. Otherwise, the wires would loose, and it may let your terminal block superheating and broken then damage your machine.
If you search the Terminal Block on the Internet, you may find that there are many Screw to Screw types. However, we also manufacture Screw to Tab, Screw to Stud and Stud to Stud type. You can visit our website and get more information about our TGP series terminal block connector:https://www.terminalsblocks.com/en/category/Terminal-Blocks/Terminal_Blocks.html
Q:How can I make payment to“SHINING”?
A:Our sales term is“T/T in advance”.However,it is okay for us to receive your payment via PayPal,Credit Card,and Western Union if you need.
Our sales team will proivde you more information once the sales term is confirmed.
Q:Do you have Cover for Terminal Block?
A:Yes,most of our Terminal Block is attached Cover.Some Terminal Blocks are attached Transparent Cover(Soft Type),some Terminal Blocks are attached Preotective Cover(Hard Type).
Please contact our sales terms for the further information if you need.
Are you curious about fuse blocks and what they do? Wondering how to properly install and troubleshoot them? In this article, we'll explain everything you need to know about fuse blocks. From their function and components to wiring and common issues, we've got you covered.
So, whether you're a DIY enthusiast or just want to learn more, read on to discover the INs and OUTs of fuse blocks. Contact SHINING right now please feel free to contact us, and we will reply as soon as possible.
The Function of a Fuse Block
A Fuse Block is a simple yet effective way to safeguard your electrical system from potential hazards. You'll be amazed at how a fuse block functions in your electrical system. This small device plays a crucial role in protecting your electrical circuits from overloading and short circuits.
The fuse block is essentially a junction box that contains multiple fuses, each connected to a specific circuit. When an electrical overload or short circuit occurs, the fuse in that circuit will blow, interrupting the flow of electricity and preventing any further damage.
This is because the fuse is designed to melt when it detects excessive current, breaking the circuit and cutting off the power supply. Once the faulty circuit is repaired, you simply need to replace the blown fuse with a new one to restore power.
Components of a Fuse Block
Material | function | Installation | |
fuse holder | Non-conductive material (ex: plastic、ceramic) | To ensure that the electrical current is properly directed | Holds the fuse in the main place |
fuse clips | Conductive material (ex: brass 、copper) | To allow for the flow of electrical current | Securely holding the fuse in place within the fuse holder |
cover | Durable material (ex: plastic) | Prevents any accidental contact with the fuse | Provide protection to fuse block |
Understanding Fuse Block Wiring
To properly understand fuse block wiring, you'll need to grasp the basic components and their functions. Once you have identified the fuse block, which houses the fuses and relays, you can start examining the wiring.
- It's crucial to ensure that the wiring is properly connected and secured to prevent any electrical malfunctions.
- The wiring is color-coded, making it easier to identify and troubleshoot any issues.
- Each fuse in the block is responsible for protecting a specific circuit from overloading or short-circuiting.
The wiring in a fuse block connects the electrical components in a circuit to the power source and allows for the flow of electricity. Understanding fuse block wiring is essential for maintaining a safe and functional electrical system in your vehicle or any other application.
Importance of Proper Fuse Block Installation
Properly installing the fuse block is crucial for ensuring the safe and efficient operation of your electrical system. When the fuse block is installed correctly. This helps to avoid damage to :
- Preventing excessive current flow in the event of a fault or overload
- Avoid damage to your system and potential hazards such as electrical fires
- Reducing the risk of loose connections causing electrical arcing or intermittent power issues
- Proper installation ensures that the fuse block is securely mounted and connections are tight
- Help to maintain the reliability and longevity of your electrical system
It's important to follow the manufacturer's instructions and guidelines when installing the fuse block, as improper installation can lead to malfunctions and safety risks. Contact SHINING right now! Please feel free to contact us, and we will reply as soon as possible.
Troubleshooting Common Fuse Block Issues
Blown fuses | A common issue with fuse blocks is blown fuses. When a fuse blows, it interrupts the flow of electricity to the circuit it protects, causing the corresponding component to stop working. To troubleshoot this problem, you can visually inspect the fuse block and look for any blown fuses. If you find a blown fuse, you can easily replace it with a new one of the same amperage rating. |
Loose or corroded connections | Another common issue is loose or corroded connections in the fuse block. This can cause intermittent electrical problems or complete loss of power to certain components. To fix this problem, you can tighten any loose connections or clean any corrosion using a wire brush or contact cleaner. |
Frequently Asked Questions
Can a Fuse Block Be Used for Both AC and DC Circuits?
Yes, a fuse block can be used for both AC and DC circuits.
It provides protection by interrupting the flow of current when there's an overload or short circuit, preventing damage to your electrical system.
How Do You Choose the Appropriate Fuse Rating for a Fuse Block?
Make sure the fuse rating is slightly higher than the circuit's maximum current.
To choose the appropriate fuse rating for a fuse block, you need to consider the current requirements of the circuit.
Can a Fuse Block Be Used for High-Powered Appliances or Equipment?
Yes, a fuse block can be used for high-powered appliances or equipment.
It helps protect them by preventing excessive current flow and acts as a safety mechanism in case of electrical faults.
Are Fuse Blocks Weatherproof or Suitable for Outdoor Installations?
Yes, fuse blocks can be weatherproof and suitable for outdoor installations.
They're designed to protect electrical circuits from overloads and short circuits. This makes them a reliable choice for outdoor use.
Can Multiple Fuse Blocks Be Connected Together to Manage a Larger Number of Circuits?
Yes, you can connect multiple fuse blocks together to manage a larger number of circuits.
This allows for a more efficient and organized distribution of power throughout your electrical system.
Conclusion
In conclusion, a fuse block is an essential component in electrical systems as it helps protect circuits from overloading and short circuits. It consists of various components, such as fuses, terminals, and wiring, that work together to ensure the safe operation of electrical devices.
Proper installation and understanding of fuse block wiring are crucial to avoid potential issues. If any problems arise, troubleshooting common fuse block issues can help identify and resolve them effectively.
Contact SHINING right now! Please feel free to contact us, and we will reply as soon as possible.

If you've ever wondered what solid state relays (SSR) are and how they work, this article has got you covered. We'll delve into the basics of SSR and explore their advantages over electromechanical relays.
Whether you're looking to understand their applications or choose the right SSR for your needs, this article will provide you with the essential information you need.
So, let's get started and demystify the world of solid state relays.Our engineers are ready to discuss your project with you contact SHINING right now!!
The Basics of Solid State Relays (SSR)
SSRs are commonly used in applications where fast switching, high reliability, and noise immunity are required, such as industrial automation, power distribution systems, and HVAC controls.
To understand the basics of SSRs, you need to know how they work and what their main components are.
Control circuit | Switching device |
Receives the input signal and activates the switching device | Controls the flow of current through the load |
Solid State Relays, or SSRs, are electronic switches that use semiconductor devices to control the flow of current. Unlike traditional electromechanical relays, SSRs don't have any moving parts. Instead, they use optocouplers or power transistors to turn on or off the flow of electricity.
How Solid State Relays (SSR) Work
- control the flow of current
Solid state relays (SSRs) work by using semiconductor devices and electronic components to control the flow of current. Unlike traditional electromechanical relays that use mechanical contacts to switch the current, SSRs utilize solid-state components such as thyristors or transistors.
- input signal is applied
When an input signal is applied to the control circuit of the SSR, the semiconductor device is triggered and allows current to flow through the output circuit. This allows SSRs to provide fast and reliable switching without the need for moving parts, resulting in longer lifespans and improved performance.
Additionally, SSRs offer advantages such as silent operation, reduced arcing, and enhanced resistance to shock and vibration. These features make SSRs suitable for a wide range of applications, including industrial automation, power distribution, and motor control.
Advantages of Solid State Relays (Ssr) Over Electromechanical Relays
You'll appreciate the numerous advantages of SSRs over electromechanical relays.
Feature | Solid State Relays (SSR) | Electromechanical Relays |
---|---|---|
Operating Principle | Based on semiconductor components, no mechanical moving parts | Operates using electromagnetic coils and mechanical contacts |
Switching Speed | Microseconds or milliseconds | Milliseconds or longer |
Service Life | Generally rated for millions of switching cycles | Limited lifespan, typically rated for thousands of switching cycles |
Weight | Light, compact | Heavier, larger |
Power Consumption and Heat Generation | Low power consumption, minimal heat generation | Higher power consumption, generates more heat |
Silent Operation | Noiseless operation | May have contact bounce or noise |
Vibration and Shock Resistance | Resistant to vibration and shock | Less resistant to vibration and shock |
Current Types Supported | Available for both AC and DC applications | Available for both AC and DC applications |
Moisture and Dust Resistance | Good moisture and dust resistance | Lower moisture and dust resistance |
Applications of Solid State Relays (SSR)
You can find SSRs used in a wide range of applications, including industrial automation, HVAC systems, and medical equipment.
- In industrial automation, SSRs are used for controlling motors, pumps, and other electrical loads. They provide fast and reliable switching, reducing the risk of damage to sensitive equipment.
- HVAC systems, where they control the heating, ventilation, and air conditioning units. They offer precise temperature control and help to optimize energy efficiency.
- In medical equipment, SSRs are used for controlling various devices such as surgical instruments, diagnostic equipment, and patient monitoring systems. Their compact size, low noise, and high reliability make them ideal for medical applications.
Choosing the Right Solid State Relay (SSR) for Your Needs
- Define Your Requirements: Begin by assessing your voltage and current requirements, as well as the type of load you will be controlling.
- Input Control Voltage and Current: Consider the input control voltage and current, as well as the output switching voltage and current capabilities of the SSR. Choose an SSR that can handle the maximum voltage and current levels of your application to ensure safe and efficient operation.
- Switching Speed and Response Time: Take into account the switching speed and response time of the SSR, as it can impact the overall system performance.
- Built-In Protection Features: Look for SSRs with built-in protection features such as overvoltage protection, short-circuit protection, and thermal protection to safeguard against potential damage.
- Size and Mounting Options: Finally, consider the size and mounting options of the SSR to ensure it can be easily integrated into your system.
These key points can assist you in choosing an SSR that aligns with your specific requirements and offers reliable performance.Contact SHINING right now!!
Frequently Asked Questions
Can Solid State Relays Be Used in Hazardous Environments?
Yes, solid state relays can be used in hazardous environments.
They have no moving parts, which reduces the risk of sparks or fires.Additionally, they are more resistant to shock and vibration.
What Are the Common Failure Modes of Solid State Relays?
Common failure modes of solid state relays include:
- Short-circuiting
- Overheating
- Voltage spikes
These issues can lead to:
- Malfunctions
- Damage to connected devices
- Potential safety hazards
Regular monitoring and maintenance are crucial to prevent these failures.
Can Solid State Relays Replace Electromechanical Relays in All Applications?
Solid state relays (SSRs) can replace electromechanical relays in many applications.
They offer several advantages, such as faster switching speeds, longer lifespan, and reduced noise.However, it's crucial to consider the specific requirements of your application before making the switch.
Are Solid State Relays More Expensive Than Electromechanical Relays?
Solid state relays can be more expensive than electromechanical relays.
However, they offer benefits such as faster switching speeds and longer lifespan.It is important to consider your specific application and budget when choosing between the two.
How Do You Determine the Appropriate Heat Sink Requirement for a Solid State Relay?
To determine the appropriate heat sink requirement for a solid state relay, you need to consider factors like:
- The maximum current
- The ambient temperature
- The thermal resistance of the relay.
These factors are crucial because they directly impact the amount of heat that the relay will generate during operation. By properly evaluating these factors, you can calculate the heat sink requirement that will effectively dissipate the heat and prevent the relay from overheating.
Firstly, you need to determine the maximum current that the relay will handle. This information is usually provided in the relay's datasheet. The higher the current, the more heat the relay will generate.
Next, you need to consider the ambient temperature in which the relay will operate. This is the temperature of the surrounding environment. Higher ambient temperatures will increase the heat load on the relay, requiring a more efficient heat sink.
Finally, you need to take into account the thermal resistance of the relay. This is a measure of how easily heat can flow from the relay to the surrounding environment. A lower thermal resistance value indicates better heat dissipation.
Once you have gathered all these factors, you can use them to calculate the heat sink requirement. This requirement is usually expressed as a thermal resistance value, indicating the maximum allowable temperature rise above the ambient temperature.
Conclusion
So there you have it - solid state relays (SSRs) are a reliable and efficient alternative to electromechanical relays. They work by using semiconductor technology to switch electrical currents, offering several advantages such as faster response times and longer lifespan.
SSRs find applications in various industries and can be chosen based on specific needs. Consider using SSRs for your electrical switching needs to enjoy their benefits and improve your system's performance.Contact SHINING right now!!
Reference
- What Is Solid State Relays(SSR)?: https://blog.shiningtw.com/terminal-blocks/48/
Image Source: Unsplash
Overview
In electrical installations, it's essential to choose the amp rating of a terminal block carefully. This rating plays a critical role in guaranteeing the safe and effective performance of your electrical system. Terminal blocks connect multiple wires, facilitating convenient and orderly connections. They establish secure and dependable links, preventing the risk of loose or exposed wires that might cause electrical dangers. Nevertheless, if the amp rating of the terminal block isn't suitable for the current it handles, it can lead to problems such as overheating, wire damage, and even the potential for fires.
Understanding Amp Rating
When it comes to electrical systems, understanding the amp rating of a terminal block is crucial. The amp rating refers to the maximum amount of current that a terminal block can safely handle without overheating or causing damage. It is an important factor to consider when selecting a terminal block for any electrical application.
What is Amp Rating?
The amp rating is a measure of the current-carrying capacity of a terminal block. It indicates the maximum amount of electrical current that can flow through the terminal block without exceeding its temperature limits. The higher the amp rating, the more current the terminal block can handle.
In electrical systems, different devices and components require specific amounts of current to operate efficiently and safely. Therefore, it is essential to choose a terminal block with an appropriate amp rating that matches the requirements of the connected devices.
How Current Relates to Amp Rating
Current and terminal blocks | The selection of an appropriate amp rating for a terminal block depends on the amount of current flowing through it. Current is measured in amperes (A) and represents the rate at which electric charge flows through a circuit. The higher the current, the greater the demand on the terminal block. |
current expected in your electrical system | To ensure proper functioning and prevent overheating or damage, it is crucial to choose a terminal block with an amp rating that exceeds or matches the maximum current expected in your electrical system. Failure to do so can lead to issues such as voltage drops, excessive heat generation, and even component failure. |
current relates to amp rating | Think of current as water flowing through a pipe. The pipe's diameter represents the amp rating – wider pipes allow more water (current) to flow smoothly without restrictions or pressure build-up. Similarly, choosing a terminal block with a sufficient amp rating ensures that there are no bottlenecks or limitations on current flow within your electrical system. |
safety and efficiency of your electrical system | It's important to note that exceeding a terminal block's amp rating can have severe consequences. Overloading a terminal block with excessive current can cause it to overheat, melt insulation, and potentially lead to electrical fires or equipment failure. Therefore, selecting the correct amp rating is crucial for maintaining the safety and efficiency of your electrical system. |
Notices
When choosing the amp rating for a terminal block, there are several factors that need to be taken into consideration:
Maximum current | This can be determined by calculating the total current drawn by all connected devices or by referring to the specifications provided by manufacturers. It is important to note that exceeding the maximum amp rating of a terminal block can lead to overheating and potential damage. |
Ambient temperature | High temperatures can affect the performance of a terminal block and may require a higher amp rating to compensate for increased heat dissipation. Additionally, if there are any voltage spikes or surges in your electrical system, it is important to choose a terminal block with an appropriate amp rating that can handle these fluctuations without causing any damage. |
Future expansions | If you anticipate any changes in your load requirements, it is advisable to choose a terminal block with a higher amp rating than what is currently needed. This will allow for flexibility and prevent the need for replacing or upgrading the terminal block in the future. |
Additional considerations | It's worth noting that selecting an overly high amp rating for your terminal block can also have drawbacks. Larger terminals blocks with higher ratings tend to be physically larger in size, which may not be suitable for certain space-constrained installations. Additionally, higher amp ratings may come at a higher cost, so it is important to strike a balance between the required amp rating and practicality. |
Factors to Consider
When it comes to choosing the right amp rating for a terminal block, there are several factors that need to be considered. These factors include voltage and current requirements, temperature considerations, wire size, and gauge. By taking these factors into account, you can ensure that you select the appropriate amp rating for your specific application. Our engineers are ready to discuss your project with you contact SHINING right now!!
Voltage and Current Requirements
One of the most important factors to consider when selecting the amp rating for a terminal block is the voltage and current requirements of your electrical system. The amp rating represents the maximum amount of current that a terminal block can safely handle without overheating or causing damage.
Maximum current that will flow through the terminal block in your system. This can be determined by calculating the total current draw of all connected devices or by consulting the specifications provided by your equipment manufacturer.
At the same time, It's crucial to choose a terminal block with an amp rating that exceeds the maximum current draw in order to prevent overheating. Selecting a terminal block with too low of an amp rating can lead to excessive heat buildup, which can cause damage to both the terminal block and connected devices. Shining is a professional Terminal Block Manufacturer in Taiwan, with full of experience.
Temperature Considerations
Another important factor to consider when choosing an amp rating for a terminal block is temperature. The operating temperature range of a terminal block plays a significant role in determining its ability to handle current safely.
When selecting a terminal block, it's essential to consider both ambient temperature (the temperature of the environment where it will be installed) and internal temperature (the temperature generated by current flowing through the terminals). Excessive heat can cause degradation of insulation materials and increase resistance, leading to potential failures or even fire hazards.
To ensure safe operation, it's recommended to choose a terminal block with an amp rating that is suitable for your specific operating temperature range. Manufacturers typically provide guidelines on how their products perform under different temperatures, so make sure to consult these specifications before making a decision.
Wire Size and Gauge
The size of the wire refers to its diameter, while the gauge represents the thickness of the wire. The wire size and gauge also play a crucial role in determining the appropriate amp rating for a terminal block.
As current flows through a wire, it encounters resistance, which generates heat. If the wire is too thin or has insufficient gauge, it may not be able to handle the current without overheating. This can lead to voltage drops, reduced efficiency, and potential damage to both the wire and terminal block.
When selecting an amp rating for a terminal block, it's important to ensure that it matches or exceeds the maximum current capacity of the wire being used. Choosing a terminal block with an insufficient amp rating can result in overheating and potential failure of both the wire and terminal block.
Additionally, it's essential to consider any future expansions or modifications to your electrical system that may require larger wires. By choosing a terminal block with a higher amp rating than your current requirements, you can accommodate future changes without needing to replace the entire terminal block.
Common Mistakes to Avoid
When it comes to choosing the right amp rating for a terminal block, there are several common mistakes that people often make. These mistakes can lead to various issues, including electrical failures and safety hazards. To ensure the optimal performance and safety of your electrical connections, it is important to avoid these common pitfalls. Our engineers are ready to discuss your project with you, contact SHINING right now!!
Underestimating Current Requirements
To avoid this mistake, it is crucial to accurately determine the required amp rating for your terminal block. This involves calculating the total current that will be passing through the terminal block by considering all connected devices and their respective current ratings. It is recommended to consult with an electrical engineer or refer to relevant specifications and guidelines provided by manufacturers.
- overheating
- melting of insulation
- fire hazards
Ignoring Temperature Considerations
Another common mistake is ignoring temperature considerations when selecting the amp rating for a terminal block. The amp rating of a terminal block is typically specified at a certain temperature, usually 20°C (68°F). However, as current flows through a terminal block, it generates heat due to resistance in wires and connections. This heat can cause an increase in temperature within the terminal block itself. By properly assessing these temperature conditions, you can select a suitable amp rating that can handle both normal operating currents and any potential temperature rise.
Ignoring temperature considerations can lead to overheating and premature failure of the terminal block. It is important to account for this heat generation by considering factors such as :
- ambient temperature
- ventilation
- proximity to other heat sources
- enclosed spaces
Neglecting Wire Size and Gauge
If the wire size is too small or the gauge is not appropriate for the intended current, it can lead to :
- potential overheating
- voltage drop
- excessive resistance
By avoiding these common mistakes, you can ensure that you choose the right amp rating for your terminal block. Taking into account accurate current requirements, temperature considerations, and appropriate wire size and gauge will help prevent issues such as overheating, electrical failures, and safety hazards. This involves considering factors such as conductor material, insulation type, length of wire, and permissible voltage drop. It is recommended to consult electrical codes and standards or seek guidance from professionals to ensure compliance and safety.
Choosing the Right Amp Rating
Shining is a professional Terminal Block Manufacturer in Taiwan, with full of experience. We will follow the guidelines to select the right ampere rating for your specific application
1. current requirements of your electrical circuit: When choosing an amp rating is the current requirements of your electrical circuit, you need to determine the maximum current that will flow through the terminal block. This can be done by calculating the total current draw of all connected devices or by referring to the specifications provided by the manufacturer
2. temperature rise of the terminal block: As current flows through a conductor, it generates heat due to resistance. If the current exceeds the amp rating of the terminal block, it can cause excessive heat buildup and potentially lead to overheating or even melting of the components. Therefore, it is crucial to choose an amp rating that can handle the expected current without exceeding its temperature limits.
3. consider any future expansion: In addition to current requirements and temperature rise, you should also consider any future expansion or changes in your electrical system. It is always wise to choose a terminal block with a slightly higher amp rating than what is currently required. This allows for flexibility and ensures that you won't have to replace or upgrade your terminal block if your needs change in the future.
4. specific load requirements: It's important to note that different types of loads may have different amp rating requirements. For example, resistive loads typically have lower amp ratings compared to inductive or capacitive loads due to their power factor characteristics. Make sure you understand your specific load requirements and choose an amp rating accordingly.
5. terminal block specifications and guidelines: While larger terminal blocks may generally have higher amp ratings, this is not always true across all manufacturers and models. Always refer to the manufacturer's specifications and guidelines for accurate information on amp ratings.
By carefully considering the current requirements, temperature rise, future expansion, load characteristics, and manufacturer specifications, you can confidently choose the right amp rating for your terminal block. This ensures the safe and reliable operation of your electrical system while minimizing the risk of overheating or other potential issues. Remember to consult with a qualified electrical engineer or professional if you have any doubts or concerns during the selection process. Contact SHINING right now!! If you have any questions or requirements, please free to contact us, and we will reply as soon as possible.
Conclusion
In conclusion, selecting the correct amp rating for a terminal block is crucial to ensure the safe and efficient operation of electrical systems. By understanding the relationship between current and amp rating, you can make informed decisions when choosing the right amp rating for your terminal block. Factors such as the maximum current load, temperature rise, and voltage drop should be carefully considered to prevent any potential issues or hazards.
In summary, selecting the correct amp rating for a terminal block requires careful consideration of various factors and adherence to industry standards. By choosing an appropriate amp rating, you can optimize the performance and safety of your electrical systems. Contact SHINING right now!! If you have any questions or requirements, please free to contact us, and we will reply as soon as possible.
Situated at the core of these electrical systems, these relays, which are frequently underestimated, have a substantial impact on safeguarding the appliance by reducing or entirely averting risks associated with electrical faults. This article seeks to underscore their significance by providing a thorough insight into these devices and elucidating their operational functions.
What are Electrical Relays?
In the expansive realm of electronics, the term 'relay' is frequently heard. However, the intriguing question that arises is, ""What precisely are electrical relays?"" In simpler terms, electrical relays are electromechanical switches that manage the functioning of an electrical circuit. As a knowledgeable operator of numerous electrical devices, comprehending the role of relays can significantly bolster your practical understanding.
Factually, these handy devices serve many purposes, such as amplifying signals, offering electrical isolation, and managing multiple circuits. They function behind the scenes, detecting and responding to specific voltage or current changes by a controlled, fluid switch action.
Here's an interesting of the key characteristics of these :
- Low power consumption: Relays are known for their energy efficiency, which aids in lowering the overall power consumption of the device they are incorporated in.
- Multiple control possibilities: These devices can manage multiple circuits simultaneously—quite an attribute when dealing with complex electrical systems!
- Reliable and sturdy: Thanks to their robust construction, relays offer longevity and reliability, enabling their use in harsh environments.
Role of Electrical Relays in Circuit Protection
Before we dive into the details, let's first grasp the essence of electrical relays. In simple terms, a relay is an electromechanical device that either opens or closes a circuit in response to the flow of current. Think of them as the 'traffic cops' of the electrical realm, guiding the current flow to avert traffic (current) jams that could result in accidents (short circuits and appliance damage).
- Overcurrent Protection: The relay operates when the current passing through the circuit exceeds a predetermined limit. It automatically interrupts the circuit, thereby preventing any potential damage to the connected appliances.
- Voltage Regulation: Electrical relays regulate voltage levels to guarantee that the connected equipment receives a stable, non-detrimental voltage supply.
- Switching Operations: They facilitate the control of high-power circuits using low-power signals without the need for physical intervention.
Types of Electrical Relays
Electrical relays are essential components in numerous electronic systems, playing a pivotal role in ensuring the correct and safe flow of power. They are available in various types, each tailored for specific applications. Gaining an understanding of the diverse types of electrical relays and their respective functions can offer a comprehensive view of their contributions to the significant advancements in today's technology.
Electromechanical Relay | The first type of relay we will discuss is the electromechanical relay. It is one of the earliest forms of electrical relays and is still present in many modern systems today due to its reliability. The electromechanical relay operates on a straightforward principle: it utilizes a magnetic field generated by electricity to actuate mechanical components. This type of relay can handle a substantial amount of current with a relatively smaller input current. |
Automotive Relay | Next on our list is the automotive relay. This relay is specifically engineered to operate under the demanding conditions commonly encountered in automotive environments, which often include high temperatures and vibrations. It is responsible for controlling various automotive systems, including air conditioning, power windows, and car lighting. |
Protective Relay | Industrial relays are designed to control heavy-duty equipment and machinery, often found in factories and power plants. Safety and reliability are of paramount importance in these environments, highlighting the need for high-quality relays. |
Electric Vehicle (EV) Relay | As the world transitions to more environmentally friendly modes of transportation, the role of the electrical vehicle relay is becoming increasingly significant. This relay aids in the control of high-power circuits necessary for the operation of electric vehicles, thereby ensuring safety and efficiency. |
Industrial Relay | Industrial relays are designed to control heavy-duty equipment and machinery, often found in factories and power plants. Safety and reliability are of paramount importance in these environments, highlighting the need for high-quality relays. |
Solid-state relay
SHINING offers two types of solid-state relays: Single Phase SSR and Three Phase SSR. Our engineers are ready to discuss your project with you. Contact SHINING right now!! There is a large variety of goods that are not listed on the website, if you have any questions or requirements, please free to contact us, and we will reply as soon as possible.
If you have any questions regarding solid-state relays, you can refer to this article.
- APPLICATION
Solid-state relays, known as SSRs, are highly durable and capable of withstanding shocks and strong vibrations. They require minimal input drive current and can be easily integrated into computer and digital control circuits. They find extensive use in various applications, including connecting peripherals to computers, controlling high-power silicon-triggered devices, and industrial automation systems. They are employed in tasks such as temperature control and resistance furnace regulation, AC motor control, intermediate relay and solenoid valve control, photocopier, and fully automatic washing machine control, as well as managing signal lights, traffic signals, and flashers. SSRs are also widely utilized in industries like petrochemicals, instrument equipment, various machinery, electromagnetic valve control, CNC machine tools, entertainment facilities, and other automated equipment. They are especially suitable for harsh environments prone to humidity and corrosion, as well as for applications involving frequent switching.
Conclusion
For more than four decades, SHINING E&E INDUSTRIAL CO., LTD has been a trusted source of dependable, high-quality components, including relays, terminal blocks, fuse holders, and more. We have consistently evolved to meet the changing demands of an increasingly electrified world.
Whether you are a seasoned electrician or a DIY enthusiast, staying informed about these advancements can significantly benefit your projects and contribute to ""Illuminating your life – Connecting the world.""
To explore the fascinating realm of relays and other essential electrical components, we invite you to peruse SHINING E&E's extensive product catalog. Filled with a wide range of cutting-edge and reliable products, it is designed to support your efforts in creating a secure and efficient electrical environment.
Frequently Asked Questions
What is an electrical relay and how does it work?
An electrical relay is an electronic device that acts as a switch, using an electromagnetic coil to control the opening and closing of contacts. When a current is applied to the coil, it creates a magnetic field that attracts or repels the contacts, allowing or interrupting the flow of current in a circuit.
What is the role of relays in circuit protection?
Relays play a crucial role in circuit protection by monitoring and controlling the flow of current in electrical circuits. They can detect abnormal conditions such as overcurrent, overvoltage, and short circuits, and quickly disconnect the circuit to prevent damage to sensitive components or overheating.
How do relays provide overload protection?
Relays can provide overload protection by using current sensing mechanisms. When the current exceeds a predetermined threshold, the relay triggers and opens the contacts, breaking the circuit. This protects the circuit from excessive current and prevents damage to the electrical system or connected devices
Knowing how to choose the appropriate relay for your electrical endeavors is vital to guarantee the optimal and proficient operation of your devices. Whether you're an electrical engineer, an enthusiast, or a skilled individual engaged in a do-it-yourself project, this guide will walk you through the essential factors when it comes to selecting the correct relay for your electrical systems.
Understanding Relay Specifications
Relays, at their core, serve as switches; they control the flow of electrical current through systems. However, every relay has some unique functions that are suited to its specific purpose and design. Knowing how to read relay specification sheets can empower you to select the exact relay that meets your project’s requirements and enhances overall performance.
Relay specification sheets, such as the numeric relay specification sheets, contain valuable information about a relay’s key attributes. Let’s break down what you need to know:
- Voltage Ratings: The minimum voltage required for the relay to operate effectively.
- Contact Material: Represents the type of material used in the relay's contact points, influencing its conductivity and durability.
- Operating Time: The time taken for the relay to switch from a non-conductive to a conductive state.
Different Basic Types of Relays
Relays are integral components of our modern electronic world, ensuring efficient operations in various industries ranging from automotive and aerospace to telecommunications and renewable energy. Understanding the different types of relays and their functionalities is essential to that end.
General-Purpose Relays
Usually used for controlling power circuits, general-purpose relays are incredibly versatile. They operate on a simple mechanism—when current flows through the coil, it generates a magnetic field strong enough to close the contact points and turn on the connected device.
This type of relay is perfect for switching multiple loads, scanning circuits, and implementing memory since it can handle various functions simultaneously. Besides, they allow for circuit isolation, meaning that the control side is separated from the load side, enhancing the safety of electronic systems.
Automotive Relays
As the name implies, automotive relays are extensively used in automobiles, primarily for controlling larger currents needed to drive vehicle components such as headlights, fuel injectors, and air conditioning systems.
Automotive relays fundamentally have the same working principle as general-purpose relays. However, they are built to withstand the rough and tumble of vehicular applications—weather fluctuations, harsh vibrations, and concurrent heavy electrical loads.
Solid-State Relays
A more sophisticated version of relays, solid-state relays, have no moving parts and use semiconductor components to do the job—something that yields them longer lifespans and higher dependability.
Solid-state relays have a silent operation, generate less heat, and offer much faster switching times. They are optically coupled, ensuring that the input and output circuits are isolated from each other, which is a significant safety advantage in electrical circuits.
Signal Relays
Signal relays, also known as telecom relays, are miniature in size and are designed to switch signal level loads in communication systems. Their function extends beyond just switching—they act as interfaces between low-power control circuitry and high-power switched loads.
Signal relays are prized for their high sensitivity, low power consumption, and capability for high-frequency operation, making them indispensable in communication systems—be it phones, radios, or computer networks.
Protective Relays
Protective relays perform a crucial duty—monitoring electrical power systems for faults (like overloads or short circuits) and triggering circuit breakers to prevent or minimize damage.
These relays use a sophisticated set of algorithms to accurately detect even the slightest deviations from normal operation parameters. With their high sensitivities, they can respond quickly to any abnormalities, hence ensuring the stability and safety of power systems.
Factors to Consider When Selecting a Relay
Choosing the perfect relay for your project can be an uphill task. However, by narrowing down on crucial factors such as coil voltage, load voltage, current requirements, and your specific project needs, making an informed decision becomes considerably easier. Let's delve deeper into each factor to understand its importance.
Coil Voltage
Ensuring you select a relay with the appropriate coil voltage is vital. If the coil voltage is too low, the relay won't switch. Conversely, an overly high voltage can lead to overheating, which might damage the relay. Therefore, you must choose a relay with a coil voltage that matches the existing circuit voltage.
Load Voltage
Another essential consideration is the load voltage. This refers to the maximum voltage that can pass through the open contacts when the relay is triggered. Choose a device that has a higher load voltage than what your project requires. Underestimating the load voltage might lead to a peculiar situation where your circuit is complete, but the relay fails to transition power since it does not handle the required voltage.
Current Requirements
Just like the voltage, your relay must meet the current requirements of your circuit. There are two main types of current rating specifications in a relay:
- The Coil Current: The energy required to activate the relay.
- The Contact Current: The current that the contacts can carry when the relay is ON.
Your relay should possess sufficient capacity to cater to both demands without any risk of overheating or failure.
Specific Project Needs
Lastly, identifying and prioritizing your specific project needs can greatly refine your search. For instance, if you need to control multiple circuits, a multi-pole relay would be an ideal choice. Similarly, you might want a relay that offers status indication or manual override features. Understanding your project's needs will help to identify the relay that checks all boxes.
Relay Use in Various Applications
Relays remain an essential component in various applications due to their versatile and effective nature. This post will analyze how relays function in different configurations.
Automation Projects
Relays offer a seamless conduit for controlling multiple outputs from a single source. Their large switching capacity makes them invaluable within automation systems. For instance, illumination systems in large auditoriums often have controls scattered on numerous switchboards throughout the facility. This way, the lights can be managed from a central point.
- Energy Saving: In "ON" or "OFF" control systems, relays aid in conserving power by shutting down and starting areas selectively. As such, only places in use consume power.
- Scalability: Considering how small relays can control large voltage loads, they simplify the task of expanding an automation system when the need arises.
Power Systems Protection
Relays fast response and accuracy in clearing faults make them vital for secure power system operation.
- Overcurrent Tripping: Relays promptly trigger circuit breakers or fuses when they detect an overcurrent scenario, such as a short circuit or overload. In doing so, they protect equipment from damage.
- Differential Protection: These relays are in transformers and large motors, offering protection against internal faults that might not activate overcurrent protection.
Vehicle Electrical Systems
Automotive engineers worldwide favor relays for the design, control, and protection of vehicle electrical systems. Often incorporated to manage power circuits, relays in vehicles can control heavy electrical loads – such as starting engines, operating headlights, and heating systems.
Water Pump Automation
Relays can automate the pump’s operation according to the water level in the tank, saving both water and electricity. By switching the pump on/off depending on the water level, relays ensure there is always an ideal amount of water in the tank while avoiding wastage or overflow.
Relays truly govern various applications in day-to-day life and within complex systems, symbolizing the spine of electrical applications. Whether it's controlling a simple domestic device or protecting expensive power equipment, their role is irreplaceable.
Advantages of Using Relays Over Other Switch Options
Designed to switch high DC voltages, relays offer an unmatched combination of rugged durability and technological sophistication.
Advantages | Description |
absence of mechanical wear | Relays operate through an electromagnetic mechanism. This absence of physical contact during operation significantly eliminates the common issue of wear and tear seen in mechanical switches, enhancing durability. |
less risk of component failure | The simple design of the relay eliminates complex mechanical components because intricate parts might fail. |
better handling of high DC voltages | Other switches might falter due to a lack of necessary insulation or the presence of sensitive components. In contrast, relays can handle high voltages with considerable ease. |
Selecting the Right Relay Based on Specific Features
Relays are integral pieces of the electronic world, while a little insight into the distinct features of different types of relays can be beneficial. In this regard, we focus on a handful of features: Dry run protection, under current or under power detection, automatic reset, and re-start relay output.
Dry Run Protection
Dry run protection is a pivotal safety feature seen predominantly in water pumps. Relays equipped with dry run protection can sustain the functioning efficiency of your water pump by preventing situations where the pump operates without water – a state that can lead to significant damage.
Under Current or Under Power Detection
These detection systems ensure the monitored device or equipment is functioning within the required power parameters. If a drop in the current or power below a safe threshold is observed, these relays trigger an alarm or automatically shut down the system to prevent harm due to underpowered situations.
Automatic Reset
Relays possessing an automatic reset feature, also called self-reset relays, provide yet another layer of protection and convenience. These relays can get your operation back on track without manual intervention following a temporary fault or disturbance. They wait for a predetermined time interval post an anomaly before supplying power back to the device.
Re-Start Relay Output
In situations where a system faces a power outage or other external disruptions, these relays are programmed to automatically restart the system when optimal conditions return. By doing so, they ensure uninterrupted operations and reliability for appliances and industrial equipment alike.
In choosing the right relay, it is crucial to consider these unique features. Your ultimate choice will depend on the individual needs of your devices and how these relays can assist you in maintaining optimal functionality while protecting against unforeseen issues.
Relays in the Automotive Industry
While not as glamorous as a super-speed engine, relays are integral to your vehicle's functionality. These electrical devices work as switches; they control a large current circuit with a much smaller circuit, generalizing the wonders of electromagnetism for practical use. So why are relays indispensable in the automotive industry? Let's dive into that conversation.
The Power of Relays
Relays protect the circuit from any damage or overheating. There are several ways that relays contribute to the safety and efficiency of a vehicle:
- Safety and Convenience: They control the power supply, ensuring that the headlights turn on and off at the right moments, providing safety and convenience.
- Power Management: The fuel pump relays control the power supply to a vehicle's fuel pump, managing majorly the engine's power and how it functions.
- Equipment Protection: Safeguarding the vehicle's electrical equipment from unexpected power surges and shocks.
- Circuit Expansion: Car relays can control multiple individual components or systems, aiding in circuit expansion without the need for multiple switches.
Different Types of Automotive Relays
Relays come in diverse forms, each specific to unique automotive needs. Here are a few commonly used relays in the industry:
- SPDT (Single Pole Double Throw) Relay: This relay has a single circuit but two potential paths for the current. They can either be 'Normally Open' or 'Normally Closed', allowing for versatile automotive applications, like switching between high and low beam headlights.
- DPDT (Double Pole Double Throw) Relay: Ideal for controlling two different circuits, these relays are essential for complex applications that demand the control of two distinct functions simultaneously.
- Solid State Relay: These are more technologically advanced, offering longer lifespan and lower power consumption, making them an ideal choice for environmentally friendly and energy-efficient vehicles.
Of course, these are just a few of the relay types. The world of automotive relays is diverse and ever-evolving, as technology brings in more sophisticated and efficient variants.
Testing and Maintenance of Relays and Protective Systems
Flawlessly navigating the maintenance of your relays and protective systems isn't an optional affair. It’s more of a safety net that guarantees the smooth, secure functioning of your systems, even in unforeseen circumstances.
Implement a Routine Maintenance Schedule
The testing frequency often depends on the manufacturer’s recommendations, industry regulations, and the nature of the work your system performs. However, as a good rule of thumb, most relays should be tested across the following timelines:
- Electromechanical: Test every 2-3 years
- Solid State: Test every 4-6 years
- Microprocessor: Test every 6-8 years
Of course, comes with the crucial note that any significant changes in your electrical system would require an immediate inspection to ensure all components function seamlessly.
Conclusion
Choosing the right relay for your electrical projects can make all the difference between a smoothly functioning system and one that’s prone to failure. From understanding various relay specifications, and different types of relays, to factors to consider when selecting these.
Undoubtedly, relays play a significant role in automation projects, power systems protection, vehicle electrical systems, and water pump automation. Furthermore, relays offer distinct advantages over other switch options.
It's also worth noting the vital role of relays in power supply systems, the automotive industry, and industrial construction. Lastly, regular testing and maintenance of relays and protective systems are needed to guarantee long-term efficiency and safety.
With over 40 years of experience, SHINING E&E INDUSTRIAL CO., LTD provides high-quality terminal blocks, fuse holders, fuse blocks, solid-state relays, and more to fulfill your various electrical requirements. For more detailed information, do explore our comprehensive range on our website.
Frequently Asked Questions
- Can I use any relay for my electrical projects?
No, you cannot use just any relay for your electrical projects. It is important to choose a relay that is specifically designed for the intended application, taking into account factors such as voltage, current, and the type of load.
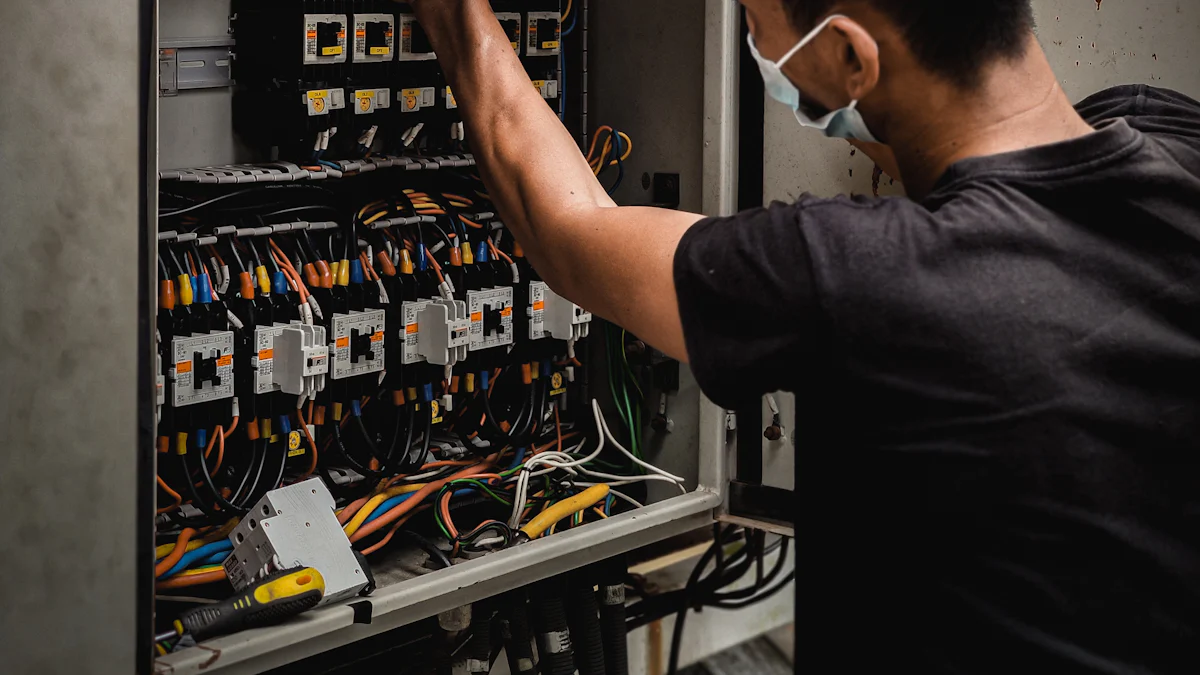
Image Source: pexels
The Importance of Testing Relay Terminal Blocks
Relay terminal blocks serve as crucial connections between control devices and loads, ensuring smooth switching and safeguarding against circuit risks. Without regular testing, these blocks may develop issues, posing a threat to equipment and safety. It's vital to include testing in your maintenance routine and during product selection.
This in-depth guide offers a systematic approach to relay testing. By adhering to these step-by-step instructions, you can promptly detect any potential issues and implement necessary measures to address them, ensuring the reliability and safety of your systems.
Common Issues with Relay Terminal Blocks
Relay terminal blocks, like any other electrical components, can experience various issues that can affect their performance. It is important to be aware of these common issues and know how to identify and troubleshoot them effectively.
Common Question | Causing Problem | How To Test |
Loose Connections | ◆Loose connections can lead to intermittent or complete failure. ◇They result in erratic behavior or even power outages. | ◆Visually inspect the junction box for physical damage or corrosion. ◇Check for tight connections free of debris. ◆Measure resistance at the connection using a multimeter to identify loose connections. (Significant deviation in resistance from the expected value indicates a loose connection.) |
Contact Welding | ◆Contact welding causes relay contacts to stick together due to excessive current or arcing. ◇This affects the proper opening and closing of contacts, impacting the relay terminal block's functionality. | ◆Visually inspect relay contacts for signs of welding or damage. ◇Look for signs of melted metal or discoloration on the contacts. ◆Use a continuity tester to check for continuity when contacts should open; the presence of continuity when it shouldn't indicate contact welding. |
Coil Failure | The coil is responsible for activating and deactivating the switching mechanism. Coil failure can lead to improper functioning of the relay terminal block. | Use a multimeter to measure coil resistance and compare the measured resistance with the specified value. If a significant difference between the measured resistance and the specified value suggests a faulty coil that needs replacement. |
By being aware of these common issues and knowing how to test for them, you can effectively troubleshoot relay terminal blocks and ensure their proper functioning.
Step-by-Step Guide to Testing Relay Terminal Blocks
Relay terminal blocks can be effectively tested by following a step-by-step approach.
Step 1: Visual Inspection
Begin by inspecting the relay terminal block for any physical damage, loose connections, or signs of contact welding. Check for any visible signs of corrosion, such as rust or discoloration. Ensure that all connections are secure and free from debris. Look for any visible signs of coil damage or overheating, such as melted insulation or burnt marks, to ensure complete protection.
Step 2: Resistance Testing
To test the relay contacts, use a multimeter to measure the resistance across them. Compare the measured resistance with the specified value provided by the manufacturer. If the measured resistance is significantly higher or lower than expected, it may indicate a problem with the contacts. Further investigation may be required to determine the cause of this deviation and take appropriate action.
Step 3: Continuity Testing
Continuity testing helps ensure that the relay contacts are making proper electrical connections when activated and breaking those connections when deactivated. Use a continuity tester to check for continuity in both states. When activated, there should be continuity between appropriate contact points, indicating a closed circuit. When deactivated, there should be no continuity between contact points, indicating an open circuit. If there is continuity in both states or no continuity in either state, it suggests a fault in the relay contacts.
Step 4: Coil Resistance Testing
The coil in a relay is responsible for activating and deactivating the switch mechanism. Measure the resistance of the relay coil using a multimeter and compare it with the specified value provided by the manufacturer. Significant differences in resistance values may indicate a faulty coil. In such cases, further investigation or replacement of the coil may be necessary.
By following this step-by-step guide, you can effectively test relay terminal blocks and identify any potential issues that may affect their performance. Remember to refer to the manufacturer's specifications for specific testing procedures and adhere to best practices for accurate and reliable results.
Best Practices for Testing Relay Terminal Blocks
1. Refer to Manufacturer's Specifications
Always consult the manufacturer's specifications for the specific relay terminal block being tested, and then you can avoid any potential errors or issues arising from improper testing techniques.
2. Use Proper Testing Equipment
Ensure that you have the necessary tools, such as a multimeter and continuity tester, to perform the required tests. It is important to use high-quality equipment that is properly calibrated to ensure precise readings. Faulty or inaccurate testing equipment can lead to incorrect results. By using reliable and well-maintained equipment, you can trust the accuracy of your test results.
3. Document and Record Test Results
Keeping a record of all test results is crucial for future reference and comparison. Documenting resistance values, continuity readings, and any other relevant data allows for easy tracking of test outcomes over time. This documentation can be useful when troubleshooting recurring issues or identifying patterns in performance. Additionally, it provides a historical record that can be referenced if further analysis or comparison is needed in the future.
By following these best practices, you can ensure accurate and effective testing of relay terminal blocks.
Conclusion
In conclusion, testing relay terminal blocks is essential to ensure their proper functioning, reliability, and excellent quality. By following a step-by-step approach and adhering to best practices, you can effectively identify common issues such as loose connections, contact welding, and coil failure through testing. Regular testing of relay terminal blocks allows for early detection of potential problems and enables prompt troubleshooting and maintenance.
If you have any questions or requirements, please free to contact SHINING, and we will reply as soon as possible.
REFERENCE

Fuse holders play a crucial role as safety mechanisms in diverse electrical and electronic circuits. While their primary function may appear simple, their significance in enhancing overall system efficiency, safety, and longevity is substantial. This article delves into the inner workings of fuse holders, examining their influence on operational conditions. It also highlights notable models currently available in the market. Additionally, we touch on the market outlook for fuse holders, reflecting the growing demand for safety components in our increasingly electrified world.
What Are Fuse Holders
Role in Electrical Circuits
When it comes to the safety and efficiency of electronic circuits, fuse holders play a pivotal role. Essentially, a fuse holder serves as a housing structure for fuses, which are integral components of most electronic devices. From home appliances and office equipment to industrial machinery and automotive systems, the applications are vast.
Using a fuse holder provides a secure place to install the fuse, which acts as a safety device to stop the flow of current in the event of an overload. Think of it as the traffic police of an electrical circuit, overseeing all electricity traveling along the path and intervening when there's too much rush, or in electrical terms, excessive current.
Having a well-functioning fuse holder in place provides numerous benefits
- Offers protection for the electronic device itself from damaging current overloads.
- Guards against potential fire hazards by stemming the excessive flow of current.
- Allows easy identification and replacement of blown fuses.
Preventing Excessive Current Flow
The primary task of the fuse holder, and indeed the fuse inside, is to prevent excessive current flow. When excessive current rushes through a circuit, it can lead to critical scenarios, such as overheating and fire hazards. This is where our key insight comes into play: fuse holders prevent potential fire hazards by controlling the excessive flow of current.
Basically, the fuse inside the holder is designed to 'blow' or fail when the current flowing through it exceeds the fuse's rated capacity. When this occurs, it creates an 'open' in the circuit, halting all current flow and thereby preventing any damage or fire due to high current or voltage.
In a nutshell, fuse holders, along with the fuses they contain, play a pivotal role in providing safety, reducing risks, and ensuring the longevity of our electronic devices. Therefore, understanding fuse holders and their function is key to ensuring the smooth operation of our electronics and mitigating risks associated with excessive current flow.
Operating Conditions Impact on Fuse Holders
In an attempt to underscore the importance of operating conditions, we're shining the spotlight on two key factors - repeated current cycling and downrating in panel-mounted arrangements. Insight into these segments provides a more holistic understanding of not only the functionality of fuse holders, but also of their longevity.
- Effects of Repeated Current Cycling
A fascinating aspect of fuse holders, and one pertinent to our discussion, is their response to repeated current cycling. Put simply, this refers to the fuse repeatedly transitioning from no current, to its maximum allowable one - a sequence that might seem ordinary but carries critical implications for fuse holders.
However, The worst-case operating conditions occur when the fuse is consistently cycled from zero current to 90% or more of the rated current. This recurrent cycling can inflict damage on the fuse holder, considerably shortening its lifespan.
- Downrating in Panel-Mounted Arrangements
Equally crucial in our quest for understanding fuse holders is the influence of downrating on panel-mounted setups. When fuse holders are mounted onto panels, there's a slight reduction in their heat transfer properties. The material of the panel often doesn't dissipate heat causing the fuse holder to retain more heat than advisable.
Given the relatively poorer heat transfer properties, fuse holders must be downrated by about 5 or 10%. This downrating could mean limiting the maximum current carry capacity to prevent overheating and subsequent damage.
Enhanced Safety Offered by Specific Fuse Holder Models
As we take a magical walk through the world of electrical systems, one of the key pieces of equipment that often receive less attention than it deserves is the humble fuse holder. Fuse holders may be small, but they play a crucial role in the safety and efficiency of any electrical setup.
Over the years, innovators and engineers have developed specific models of these essential components with a heightened focus on ensuring safety. We’ll focus on two particularly noteworthy models: SHINING SERIES CLASS FS-03XL1 Fuse Holder and the SHINING SERIES CLASS FS-03XL3Fuse Holder. Both are designed to provide top-tier safety performance in their respective applications.
- SHINING SERIES CLASS FS-03XL1 & SHINING SERIES CLASS FS-03XL3 Fuse Holder
Safety Arises from Its Design | 1. Tight and stable fuse fitting 2. Guarding against loose connections 3. Unwanted power disruptions |
Ensures Easy and Secure Handling | 1. Very user-friendly 2. Easy to install 3. Elevating operational safety |
Key Safety Parameters | 1. Comprehensive protection against electrical fire 2. Comprehensive protection circuit overloads |
Frequently Asked Questions
Why is a fuse holder important in electrical circuits?
A fuse holder is important in electrical circuits because it provides a secure and reliable way to hold and connect fuses. It ensures that the fuse is properly installed and easily replaceable if it blows due to excessive current flow.
What are the types of fuse holders available?
There are various types of fuse holders available, including panel mount fuse holders, inline fuse holders, PCB mount fuse holders, DIN RAIL Fuse holders and surface mount fuse holders. The type of fuse holder to use depends on the specific application and circuit design.
What factors should be considered when selecting a fuse holder?
When selecting a fuse holder, factors like current rating, voltage rating, fuse type compatibility, mounting method, and environmental conditions should be considered. It is important to choose a fuse holder that is suitable for the specific requirements of the circuit.
Can I replace a fuse holder myself?
Yes, in most cases, a fuse holder can be replaced by carefully following the manufacturer's instructions. However, if you are not experienced in working with electrical circuits, it is recommended to consult a qualified electrician to ensure safety and proper installation. If you have any questions or requirements, please free to contact us, and we will reply as soon as possible. Contact SHINING right now
Conclusion
From understanding the core role of fuse holders, preventing excessive current flow, to appreciating the impact of operating conditions on these components, we've sailed through pivotal aspects of fuse holder discussions.
Safety and efficiency are the heartbeats of all electrical setups, and it is here that companies like SHINING E&E INDUSTRIAL CO., LTD continue to shine. With over four decades of professional manufacturing legacy in the realms of terminal blocks, connection bars, fuse holders, fuse blocks, and more, SHINING E&E bolsters value to customers around the globe. Their products, quintessentially embodying their slogan "Light up your life - Connect the world," offer a reliable safety solution for electricity.
REFERENCE
Fuse Holders: Ensuring Safety and Protection in Electrical Circuits
Understanding Fuse Holders
Ever wondered how your appliances are protected when faced with sudden electrical surges? Enter fuse holders, the unsung heroes of the electrical realm. When things get electrically heated, these components step in to save the day. This segment aims to offer a thorough grasp of these essential elements, outlining their functions and the various types at your disposal.
What are Fuse Holders?
A fuse holder is essentially a protective case that houses a fuse. This circuit protection device serves as a sacrifice during electrical overloads, breaking the circuit and thus shielding your appliances from potential harm. It's a principle as old as electricity itself, yet as important as ever in modern systems.
Types of Fuse Holders
Choosing the right type of fuse holder is critical, and fortunately, there is a variety to suit different needs and requirements. Here's a snapshot of the most commonly used types:
In-line fuse holders | Ideal for automotive applications, these have a wire running into and out of the holder. |
Chassis mount holders | As the name suggests, these are mounted directly onto a panel, often preferred for industrial equipment. |
Rail mount holders | These are fixated on a DIN rail and are usually seen in manufacturing sectors. |
PCB mount holders | Designed to be attached to a Printed Circuit Board (PCB), these are quite common in tech devices, from laptops to gaming consoles. |
Key Function and Role in Electrical Systems
The significance of fuse holders lies in their safeguarding role within electrical systems. Their job might be straightforward, but by no means is it insignificant. By preventing electrical overflows from causing damage, they serve as the defense mechanism of an electrical system. This is essential, not just for the seamless functioning of appliances & devices, but also to prevent potential fire hazards or accidents caused by electrical failures. Making these seemingly trivial components an essential aspect of modern life.
The Importance of Quality in Fuse Holders
Electrical systems and their efficiency are one of today's highly critical elements. We undeniably require assuring the proper maintenance and protection of our electrical devices. In this landscape, fuse holders serve as an essential aspect of safeguarding our electrical systems. High-quality fuse holders are not a mere luxury but a necessity for every electrical system. Why, you ask? Let’s delve deeper into the importance of quality in fuse holders.
- Quality Material and Design
The quality of material and design in fuse holders can significantly influence electrical systems’ overall efficiency and safety. Good quality materials not only improve the product’s lifespan but also decrease the frequency of maintenance and replacements, proving cost-efficient in the long run.
Just think about it this way: Would you instead invest a little more upfront for a fuse holder with a sturdy and durable design? Or would you like to repeatedly buy cheap fuse holders and pay extra in repair costs due to system failures? The answer is quite clear, making it evident that quality material and design are paramount considerations when talking about fuse holders.
- Safety and Reliability
The underlying notion when discussing electrical systems is safety and reliability. In this aspect, top-quality fuse holders come into play. They protect the electrical systems from instances of short circuits, overcurrents, or any other electrical fault, ensuring committed functionality without interruptions.
It's worth noting that premium fuse holders adopt innovative designs that aid in dissipating heat effectively, further enhancing the system's safety. Not only does this prevent possible electrical faults from escalating, but it also safeguards your expensive electrical devices from potential dangers.
- Longevity and Performance
Incorporating high-quality fuse holders secures the longevity and optimal performance of the electrical systems. These fuse holders, made from superior materials, resist wear and tear effectively, enhancing their longevity significantly. Moreover, they exhibit higher tolerance to varying voltage levels, thereby facilitating consistent performance.
Imagine going through a vital project, and suddenly there's a system failure due to a substandard fuse holder. Wouldn't that be frustrating? Nobody fancies such unprecedented interruptions. Investing in a premium fuse holder ensures you smooth and uninterrupted electrical performance, making it quintessential for the augmentation of system efficiency.
In conclusion, the significance of quality in fuse holders can never be overstated. Now that you comprehend the role of quality fuse holders, ensure that your focus is on securing the best ones for your electrical systems. It’s about ensuring the safety and optimal performance of the system, as well as saving costs in the long run. So, the next time you are shopping for fuse holders, you will know exactly what to prioritize.
Improving Fuse Holder Quality
The fuse holder might not be the first component that comes to mind when you think of quality improvement, but it plays a crucial role in ensuring the electrical safety of various equipment. Over time, there have been significant advancements in their manufacturing processes, design attributes, and quality control standards, contributing to their overall quality enhancement.
Advancements in Fuse Holder Manufacturing
In earlier times, fuse holders were typically hand-crafted, leading to inconsistencies and discrepancies in product quality. But, with the evolution of technology, manufacturers have adopted automated production techniques that ensure uniformity and efficiency.
Some of these advancements include:
- Automation: Machines are programmed to fabricate fuse holders, reducing human error or inconsistency, and leading to enhanced precision and quality.
- Use of new-age materials: Manufacturers have started using cutting-edge materials like thermal-resistant plastics and high-grade copper for superior conductivity and durability.
- Innovative technologies: Technologies like 3D printing and Computer Numeric Control (CNC) machining have revolutionized the production of complex fuse holder designs that were once hard to achieve manually.
Designing for Durability and Safety
When it comes to fuse holders, design isn't just about aesthetics – it's about ensuring durability and safety. An ideal fuse holder design should be compact, robust, easy to handle, and, most importantly, safe to operate.
Design features like these are becoming increasingly common:
- Thermally robust materials to withstand high temperatures.
- Clear markings on the body of the fuse holder for easy identification of fuse ratings.
- Rugged construction for enduring rough handling during installation or fuse replacement.
Quality Control and Standards
Manufacturing and design alone can't guarantee the improved quality of fuse holders. Adherence to stringent quality control measures and international standards is just as imperative. Regular inspection at every stage of production, rigorous testing for physical and electrical properties, and compliance with safety norms set by organizations like UL (Underwriter Laboratories) and IEC (International Electrotechnical Commission) - all contribute to the quality of a fuse holder.
Developing, adhering, and updating such standards not only benefits the manufacturers by providing a competitive edge but also assures the end buyers that the product has been manufactured considering the safety and quality norms.
Thus, advancements in manufacturing, attention to design for safety and durability, strict adherence to quality control measures, and internationally recognized standards collectively enhance the quality of fuse holders. Consequently, this quality improvement is leading to safer and more efficient electrical systems across various sectors.
Conclusion
Regardless of the progress in technology and the evolution of electrical components, the worth of a reliable and efficient fuse holder cannot be ignored. As we extensively explored in this article, the quality of a fuse holder plays a critical role in enhancing the safety, reliability, and overall performance of an electrical system.
Choosing a high-quality fuse holder is not just an indulgence, but a requirement that can save a device, a system, or even a life. Aim for trusted brands such as SHINING E&E INDUSTRIAL CO., LTD, who have a proven track record in manufacturing durable and safe electrical components, including fuse holders. Their commitment to 'Light up your life – Connect the World' isn't just a tagline, it's a demonstration of the pivotal role their products play in all our lives.
As we step into the future, let's remember that quality matters, in everything we do and every product we use - particularly when it comes to our electrical systems that power our world. Visit SHINING E&E INDUSTRIAL CO., LTD to explore their wide selection of high-quality fuse holders and experience the difference quality can make in your electrical connections. The importance of quality fuse holders in electrical systems cannot be underestimated. Always choose wisely.
Frequently Asked Questions
What is a fuse holder and what does it do?
A fuse holder is a device that holds a fuse and provides a secure connection between the fuse and the electrical circuit. It helps protect the circuit by preventing excess current flow and acts as a safety measure in electrical systems.
Why is it important to use quality fuse holders in electrical systems?
Using quality fuse holders is crucial in electrical systems as they ensure a reliable and secure connection between the fuse and the circuit. Poor-quality fuse holders may lead to loose connections, overheating, and potential electrical hazards.
What are the characteristics of a high-quality fuse holder?
A high-quality fuse holder should have a sturdy construction, secure mounting capabilities, good electrical conductivity, and the ability to handle the rated current without overheating. It should also be compatible with the specific type and rating of fuses being used.
Can using low-quality fuse holders affect the performance of electrical equipment?
Yes, using low-quality fuse holders can negatively impact the performance of electrical equipment. Loose connections or poor conductivity can lead to voltage drops, increased resistance, and malfunctioning of sensitive electronic components.
Where can I find reliable and quality fuse holders?
You can find reliable and quality fuse holders at reputable electrical supply stores, online marketplaces, or through trusted manufacturers and distributors. Make sure to check product specifications, customer reviews, and certifications before making a purchase.
REFERENCE
The Importance of Quality Fuse Holders in Electrical Systems